Superstopy żaroodporne (HRSA) dzieli się na trzy grupy materiałowe: na bazie niklu, żelaza i kobaltu. Tytan może być czysty albo ze strukturą alfa lub beta. Obrabialność stopów żaroodpornych oraz tytanu jest słaba, zwłaszcza tych poddanych starzeniu, co nakłada szczególne wymagania na narzędzia skrawające. W przemyśle lotniczym obróbka podzielona jest na trzy etapy: Pierwszy Etap Obróbki (FSM), Pośredni Etap Obróbki (ISM) oraz Ostatni Etap Obróbki (LSM). W LSM najważniejsza jest integralność powierzchni, co ogranicza parametry skrawania i podkreśla wagę ostrych krawędzi, w celu uniknięcia tak zwanych białych warstw o odmiennej twardości i tworzenia naprężeń szczątkowych.
SPIS TREŚCI
- Kształt płytki oraz kąt przystawienia
- Glebokość skrawania
- Fazowanie wstępne
- Wymagania dotyczące chłodziwa
- Tytan
- Superstopy żaroodporne HRSA
- Przewidywana trwałość narzędzia − spiralna długość skrawania, SCL
Kształt płytki oraz kąt przystawienia
Powszechnym kryterium zużycia w tytanie i superstopach żaroodpornych jest powstawanie karbu. Dzięki wybraniu niewielkiego kąta przystawienia lub okrągłych płytek, posuw oraz trwałość narzędzia mogą być znacząco zwiększone.
Wyjątkowa płytka Xcel łączy dostępność jaką daje oprawka o kącie przystawienia 93° z wydajnością 45° kąta przystawienia przy krawędzi skrawającej przy głębokościach skrawania do 2,5 mm i jest odpowiednia do operacji półwykańczających.
Wskazówki dla uniknięcia powstawania karbu podczas obrabiania materiałów z super stopów żaroodpornych
Powstawanie karbów nie może być całkowicie wyeliminowane, lecz może ono zostać ograniczone do minimum, gdy przestrzega się następujących ogólnych reguł: • Stosować płytki okrągłe. • Należy stosować możliwie najmniejszy kąt przystawienia. • Należy uwzględniać zależność między średnicą płytki a głębokością skrawania (patrz rysunek). • Można zaprogramować wejście po łuku, w celu eliminacji potrzeby wstępnego fazowania oraz minimalizacji powstawania karbów. Będzie istniał jeden punkt styczności, w którym płytka uderza twardą zgorzelinę/powierzchnię w narożu przedmiotu obrabianego i jeden przy linii głębokości skrawania. • Zagłębianie skośne jest idealnym rozwiązaniem dla tokarek CNC. Dzięki niemu, wzdłuż krawędzi skrawającej nie rozprzestrzenia się żadne uszkodzenie. Przy zmiennej głębokości skrawania, jest to najlepsze rozwiązanie. Alternatywą mogą być wielokrotne przejścia ze zmienną głębokością skrawania. Stosując powyższe metody toczenia należy pamiętać, że głębokość skrawania nigdy nie powinna być mniejsza niż 0,25 mm ze względu na ryzyko wykruszania krawędzi.
Głębokość skrawania
Chcąc zminimalizować powstawanie karbów, najlepsze wyniki uzyskuje się stosując głębokość skrawania wynoszącą 15% (maks.) średnicy płytki okrągłej lub 15% promienia naroża płytki innej niż okrągła. Można stosować większe głębokości skrawania, lecz nigdy nie należy przekraczać 25 % średnicy płytki. Zanim takie duże głębokości skrawania będą mogły być zastosowane, obrabiany przedmiot musi być pozbawiony twardej zgorzeliny lub innej warstwy utwardzonej.
Fazowanie wstępne
Zaleca się wstępne wykonanie faz na przedmiocie podczas pracy płytkami ceramicznymi.• W celu ograniczenia zagrożenia powstawaniem zadziorów, gdy płytka wychodzi z przedmiotu obrabianego. Ma ono również pozytywny wpływ na płytkę, gdy wchodzi ona w przedmiot obrabiany.• W celu uniknięcia punktowego zużycia ostrza przy fazowaniu, należy stosować posuw prostopadły względem fazy.
Wymagania dotyczące chłodziwa
Podczas toczenia superstopów żaroodpornych lub stopów tytanu, zawsze powinno być stosowane chłodziwo, bez względu na to, czy używane są węgliki, czy ceramika. Jego ilość powinna być duża i dobrze skierowana. Wysoce precyzyjne podawanie chłodziwa (do 80 bar) stało się obecnie powszechne w nowoczesnych obrabiarkach, a dzięki technice doprowadzania chłodziwa CoroTurn HP , prędkość skrawania może być zwiększona do 20%, trwałość narzędzia do 50% oraz znacząco poprawia się łamanie wióra. Technika Jet-break wykorzystująca precyzyjnie podawane chłodziwo pod bardzo wysokim ciśnieniem (80 do 1000 bar) może być stosowana podczas używania pionowych centr tokarskich (VTL). W celu uzyskania dalszych informacji, prosimy skontaktować się z przedstawicielem Sandvik Coromant.
Tytan – Ti6Al4V (30 HRc)
Tytan
Gatunki płytek węglikowych
Gatunki węglików powinny być wybierane zgodnie z poniższą tabelą, w zależności od typu obróbki
(wykańczająca, średnia, zgrubna) oraz warunków (dobre, przeciętne, trudne). Do obróbki tytanu nie zaleca się ceramiki.
Zobacz tabelę
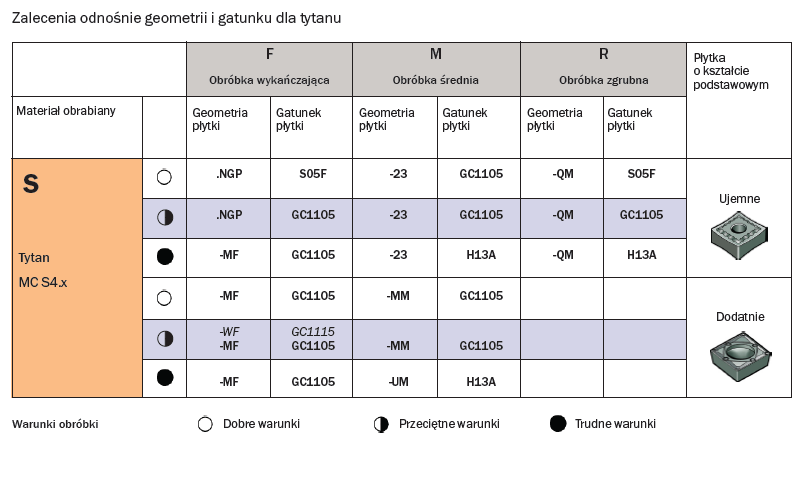
Superstopy żaroodporne
Operacja i warunki określają wybór gatunku. Obróbka zgrubna (pierwszy etap obróbki, FSM) Obróbka jest przeprowadzana w stanie wyżarzonym (ok. 26 HRc).
Płytki węglikowe:
W materiałach, gdzie skóra pochodzi z odlewania lub kucia, należy stosować płytki jednostronne o geometrii -HM lub -SR w gatunku GC2025 albo GC2015. Kąt przystawienia powinien być niewielki (nie większy niż 75°) a głębokość skrawania duża, aby dostać się pod twardy naskórek, w celu zmniejszenia powstawania karbu. Jeżeli trzeba zastosować większy kąt przystawienia to lepszym wyborem są gatunki pokrywane metodą PVD, jak GC1105 i GC1115 lub H13A dla najlepszej udarności.
Płytki ceramiczne:
Można stosować gatunek CC670 (wzmocniony whiskersami), lecz zarówno posuw fn jak i głębokość skrawania ap muszą być zmniejszone. Prędkość skrawania vc może być dużo wyższa. W celu uzyskania najlepszej trwałości narzędzia, stosować niewielkie kąty przystawienia lub okrągłe płytki.
Płytki ceramiczne: Obróbka średnia (ISM) są tym etapem, gdzie korzyści z użycia ceramiki są najbardziej oczywiste, chociaż głębokość skrawania w materiałach starzonych jest mniejsza niż podczas operacji zgrubnych (FSM). Ceramiki SiAlON posiadają wspaniałą odporność na powstawanie karbu i możliwość obróbki z dużo większymi prędkościami skrawania, vc, (150-280 m/min.) w porównaniu do gatunków węglikowych. Posuw fn może być utrzymany na wysokim poziomie (0,15-0,35 mm/obr.). Nadrzędne znaczenie ma konieczność stabilnego zamocowania i prawidłowo zastosowanego doprowadzania chłodziwa (ilość jest ważniejsza od ciśnienia). Pierwszym wyborem dla maksymalnej produktywności jest CC6060, a w bardziej niestabilnych warunkach CC6065.
Parametry skrawania – ceramikaObszary zastosowania gatunków ceramicznych
Prędkość skrawania powinna być odpowiednio dobrana, w celu wytworzenia odpowiedniego ciepła w strefie skrawania dla uplastycznienia wióra, lecz nie może być zbyt wysoka, aby nie doprowadzić do braku równowagi ceramiki. Posuw fn powinien być wybrany tak, aby zapewnić grubość wióra hex, która będzie wystarczająco wysoka, aby nie umacniać materiału, lecz nie za wysoka, aby nie powodować wykruszania krawędzi. Wyższe posuwy i głębokości skrawania wymagają zmniejszenia prędkości skrawania vc. Te granice będą zmieniać się w zależności od twardości materiału części oraz wielkości ziarna. Zalecane startowe parametry skrawania (RNGN 12, RCGX 12) – Inconel 718 (38 do 46 HRc)
Zobacz tabelę
Obróbka wykańczająca (ostatni etap obróbki, LSM) Obróbka materiałów po starzeniu, 35-46 HRc. Konieczność uzyskania niskich naprężeń szczątkowych sprawia, że płytki ceramiczne nie są zalecane, gdyż prędkości skrawania vc powinny być utrzymane poniżej 80 m/min. Innymi czynnikami wpływającymi na naprężenia szczątkowe są: • Zużycie powierzchni przyłożenia – maksymalnie 0,2 mm • Grubość wióra – maksymalnie 0,1 mm • Ostre krawędzie – preferowane są płytki szlifowane.
Płytki węglikowe: GC1105 (pokrywany metodą PVD) posiada najlepszą wytrzymałość na powstawanie karbu i stanowi pierwszy wybór gdy: • Posuw wynosi mniej niż 0,1 mm • Toczone są części cienkościenne lub smukłe • Kąt przystawienia wynosi 75° lub więcej • Nie można uniknąć długich wysięgów narzędzia. S05F (pokryty metodą CVD) daje większą trwałość narzędzia niż GC1105, gdy są stosowane małe kąty przystawienia lub płytki okrągłe.
Zalecenia odnośnie geometrii i gatunku dla superstopów żaroodpornych
Zobacz tabelę

Przewidywana trwałość narzędzia − spiralna długość skrawania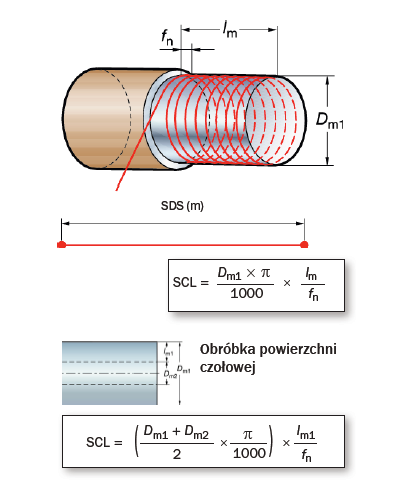
Ze względu na stosunkowo niską trwałość ostrza podczas toczenia superstopów żaroodpornych oraz materiałów z tytanu, jedna płytka zwykle wykonuje jedno przejście, zanim zostanie zmieniona. Obliczenie spiralnej długości skrawania, SCL, jest metodą przewidywania trwałości krawędzi płytki, w celu uniknięcia niepożądanych zmian płytek w połowie przejścia.
Uwaga:
• Każdy wykres SCL jest wyjątkowy i znajduje zastosowanie tylko dla danej
płytki, geometrii, gatunku, głębokości skrawania oraz materiału.
• Podczas obróbki wykańczającej ważnym jest unikanie zmiany płytki w połowie
przejścia, dlatego podajemy szereg prędkości skrawania i odpowiednie dla
nich różne długości skrawania.
• Do obróbki zgrubnej, posiadamy optymalne parametry skrawania dla
każdego typu płytki oraz odpowiadającą im spiralną długość skrawania, SCL.
Obróbka wykańczająca
Celem jest znalezienie prawidłowej prędkości skrawania, vc, która zapewni pełne przejście bez zmiany płytki. 1) Wybrać typ płytki odpowiedni do obrabianego przedmiotu.2) Użyć zoptymalizowanych ap i fn dla tej płytki.
Przykład:
CNGP 120408-1105
ap 0,25 mm, fn 0,15 mm
4) Wybrać prędkość skrawania, vc, z wykresu SCL / vc
Przykład:
CNGP 120408 1105
SCL= 1885 m = >vc = 50 m/min.
Przy vc = 50 m/min. jedna krawędź zdoła osiągnąć spiralną
długość skrawania 1885 mm odpowiadającą długości toczonego
przedmiotu, lm, 150 mm.
3) Obliczyć SCL.
Przykład:
Dm1 = 600 mm, lm = 150 mm
4) Wybrać prędkość skrawania, vc, z wykresu SCL / vc
Przykład:
CNGP 120408 1105
SCL= 1885 m = >vc = 50 m/min.
Przy vc = 50 m/min. jedna krawędź zdoła osiągnąć spiralną
długość skrawania 1885 mm odpowiadającą długości toczonego
przedmiotu, lm, 150 mm.
Źródło: „Poradnik obróbki skrawaniem” Sandvik